The steps involved in repairing your controllers in our workshops
At Normandy Control Group, we do everything in our power to ensure optimum repair of your controllers. Thanks to our workshops in France (Le Havre and Marseille) and Africa (Ivory Coast and Senegal), and our recognized expertise in Woodward systems, we offer a fast, reliable, quality service. Here’s how the repair process works in our workshops.
Care on delivery
As soon as your equipment arrives on our premises, we subject it to a rigorous initial inspection.
This initial stage includes a meticulous visual inspection and a series of rapid tests, carried out by our expert technicians in the field, enabling a preliminary diagnosis to be made.
The aim is to detect immediately any major faults or recurring problems that need to be corrected.
This information is then used to guide the next steps.
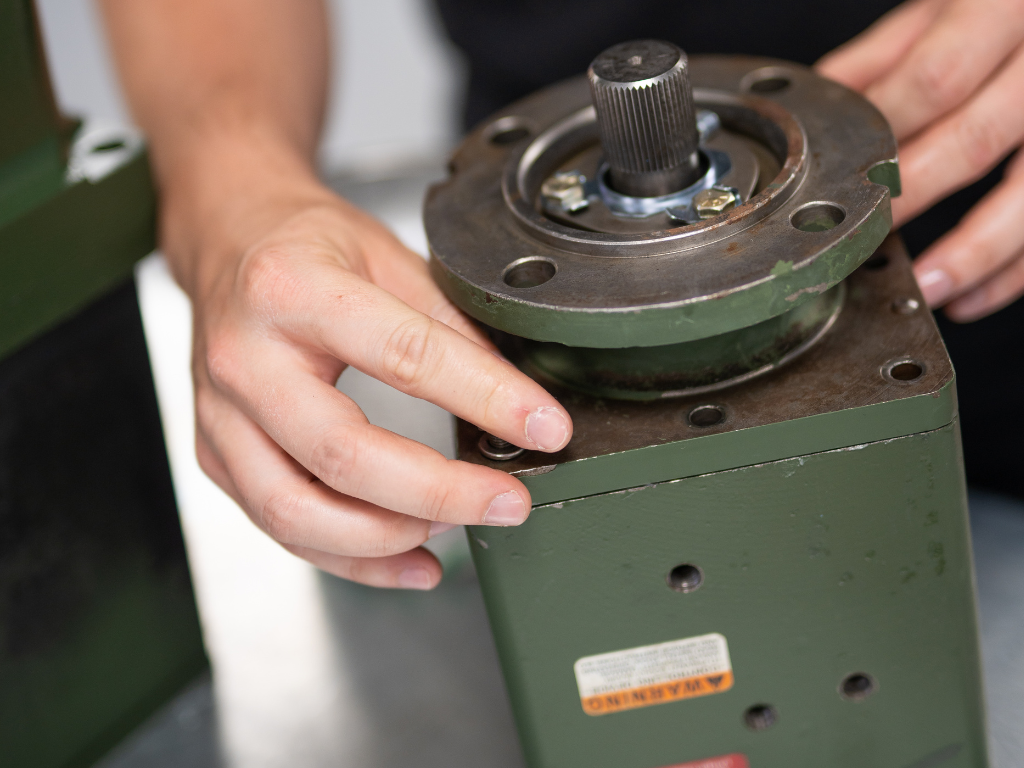
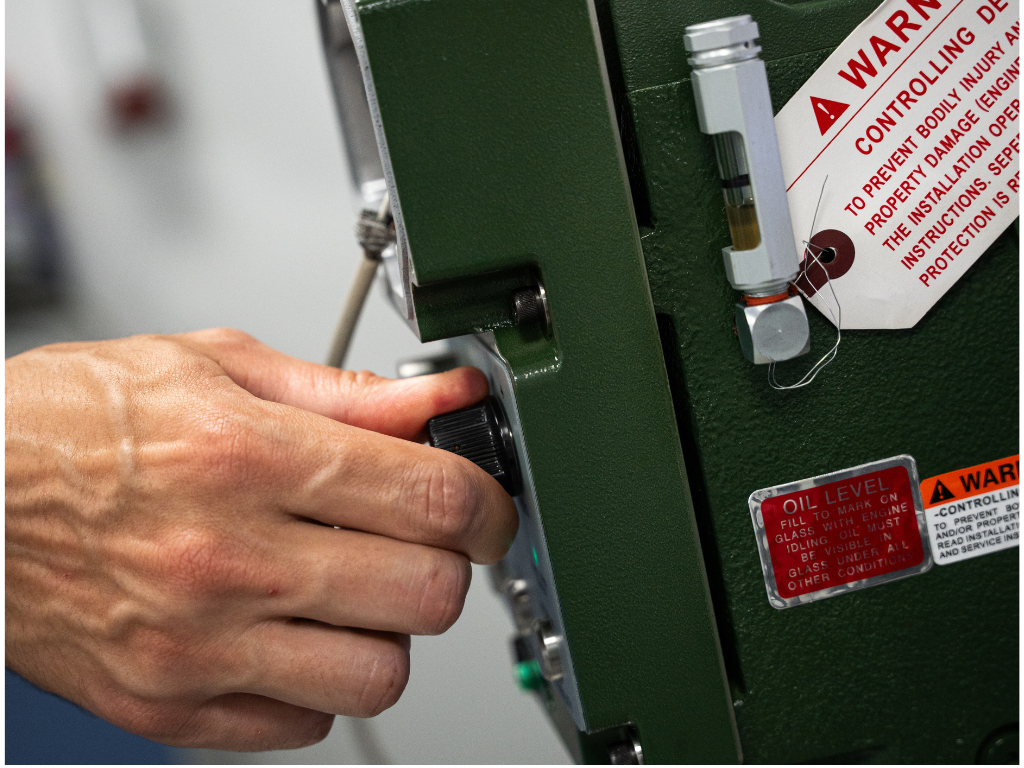
A detailed technical diagnosis
Each piece of equipment is then examined in depth by our specialized technicians. Thanks to our advanced diagnostic tools and specific test benches, we can precisely analyze the causes of malfunctions. This phase is crucial for identifying defective parts, assessing the overall condition of the equipment and drawing up an appropriate repair plan.
Our experts also take into account your specific needs, whether it’s a complete repair, reconditioning or replacement of critical parts. This customization ensures that every intervention is perfectly tailored to your operational requirements.
Repairs to the highest standards
Following your agreement, our teams will carry out repairs under controlled conditions. We use only certified parts that comply with manufacturers’ specifications. Whether for complex equipment or simpler components, every intervention is carried out with the utmost precision.
Our workshops are equipped to handle a wide range of services, including technical overhauls, complete overhauls and fine-tuning of highly technological systems. This expertise, combined with our strategic partnerships with leading brands, enables us to guarantee impeccable quality.
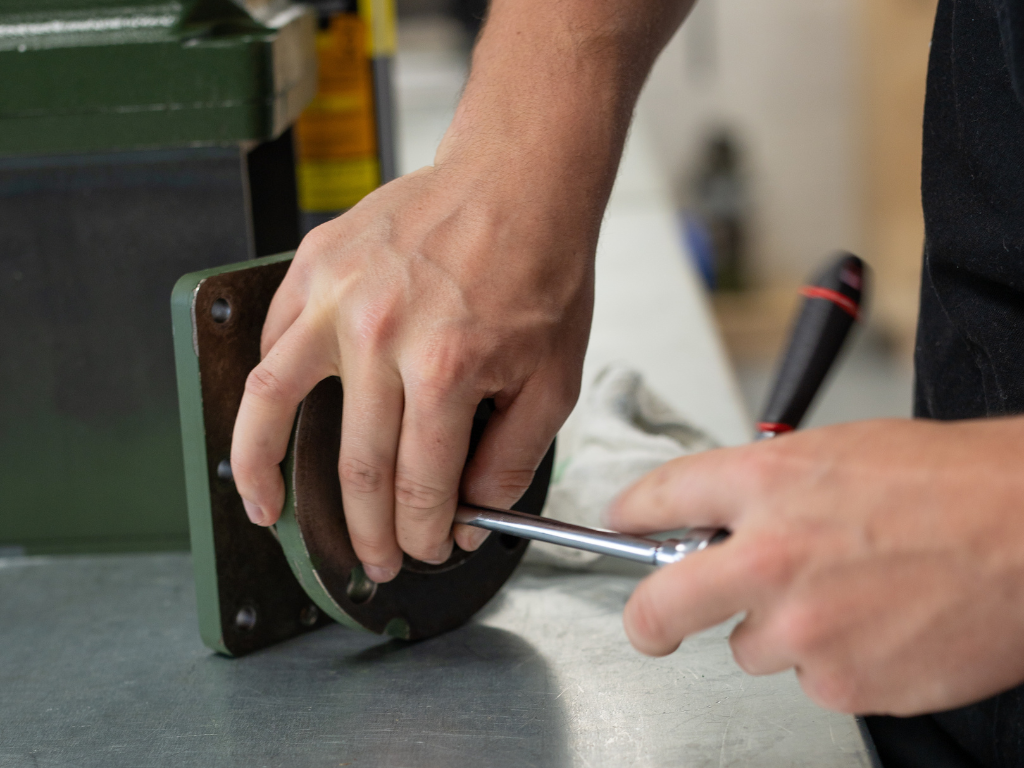
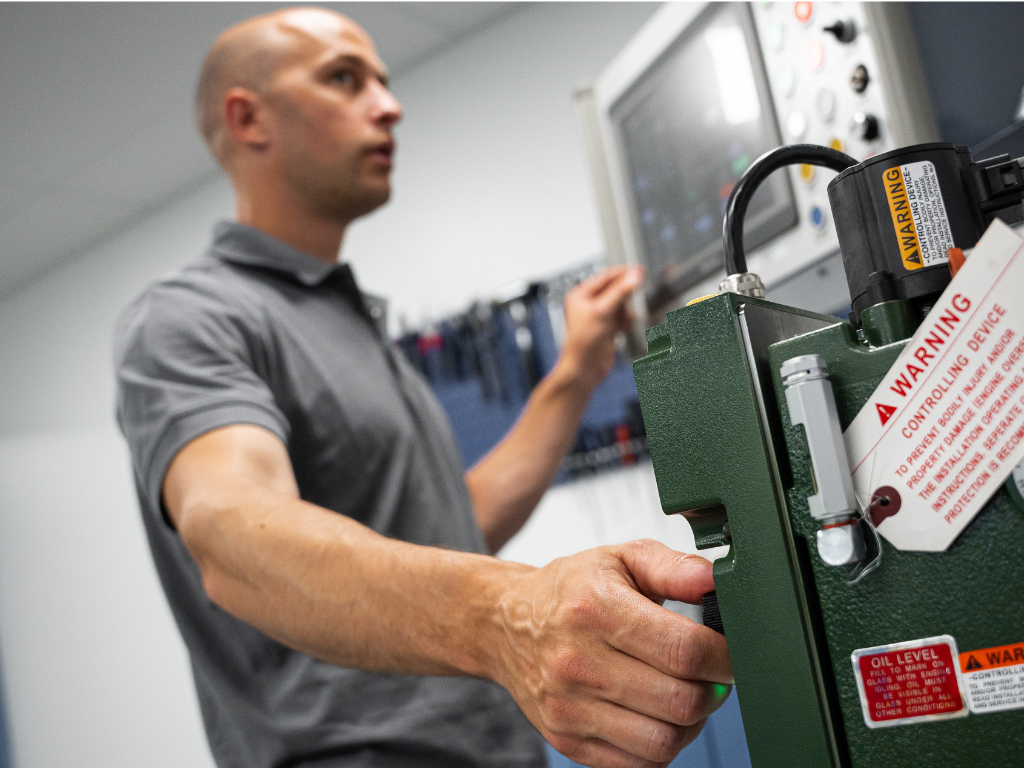
Exhaustive quality control
Before returning your equipment to you, we carry out a series of final tests to check that each component is working properly. These tests reproduce actual operating conditions to ensure that the equipment is fully operational and ready to be reintegrated into your production line.
We then provide you with a detailed report. This document summarizes the work carried out, the parts replaced and the final test results.
Fast, secure shipping
Finally, we prepare your equipment for shipment.
Each product is carefully packed to ensure smooth delivery.
Thanks to our optimized logistics, we ensure that your equipment is quickly available, wherever you do business.
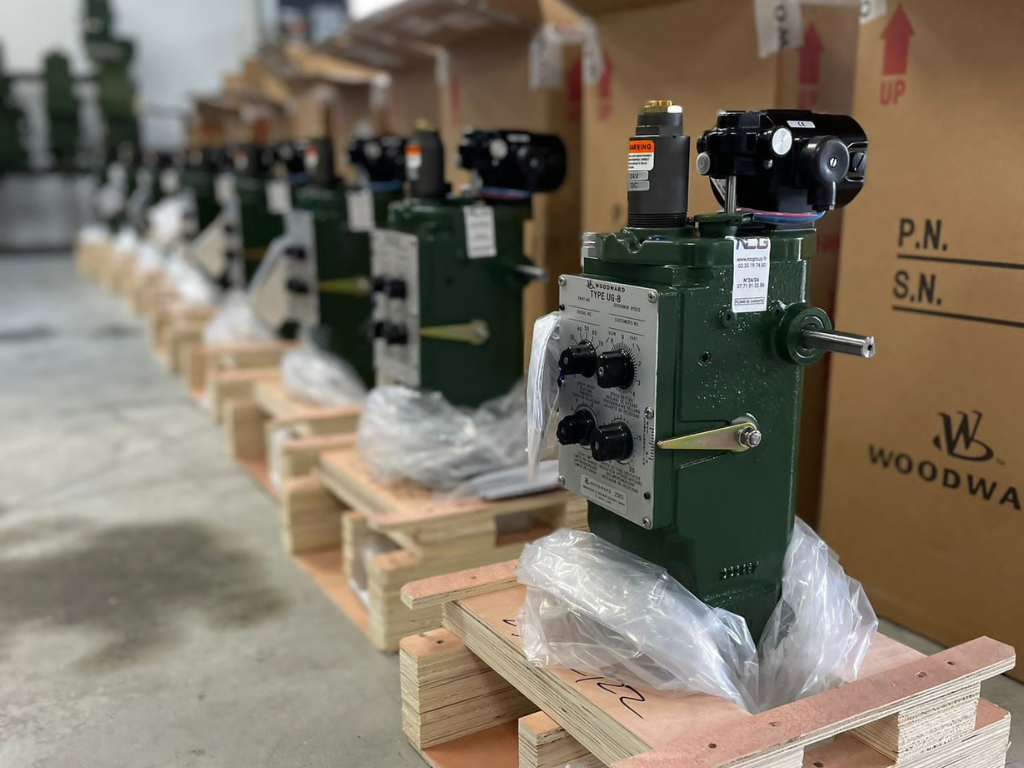
Why call on Normandy Control Group/NCG?
When you choose Normandy Control Group, you choose a partner you can trust for the maintenance and repair of your industrial equipment. As an official Woodward and Parker Meggitt (vibro-meter) distributor in France and French-speaking Africa, including Algeria, Tunisia and Morocco, we offer recognized expertise in the field. We also have two workshops in France, in Le Havre and Marseille, as well as workshops in Côte d’Ivoire and Senegal.