An essential strategy for preventing mechanical breakdowns
In industry, rotating machines are at the heart of many critical processes. Motors, turbines, alternators, compressors or pumps often operate continuously, under demanding conditions. Over time, such equipment can develop mechanical faults invisible to the naked eye, but perceptible through analysis of their vibrations.
Vibration monitoring involves measuring these mechanical signals and analyzing their variations. Excessive or irregular vibration may reveal an imbalance, a bearing fault, a lubrication problem or shaft misalignment. By detecting these symptoms at an early stage, it is possible to intervene before a major malfunction occurs.
Without this kind of monitoring, signs of wear go unnoticed until a breakdown occurs, often suddenly. The cost of repair is then much higher, not to mention the impact on production and safety.
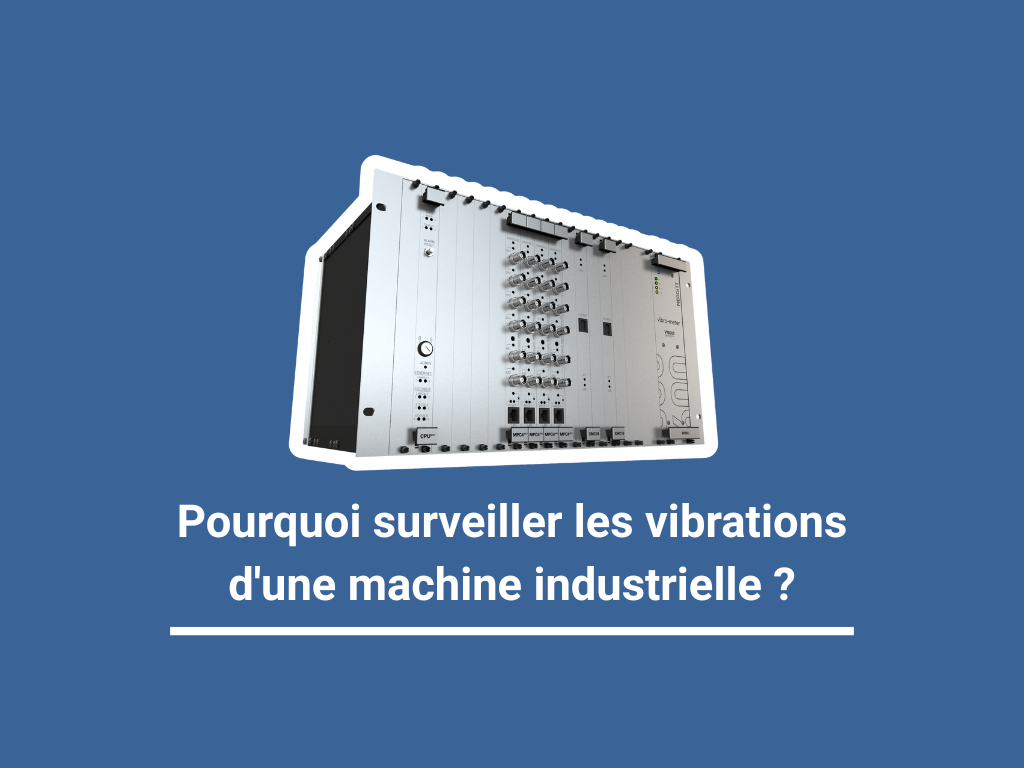
Reduce unscheduled downtime and optimize maintenance costs
One of the main objectives of vibration monitoring is to avoid unplanned shutdowns. By integrating vibration sensors into a supervision system, maintenance managers obtain real-time data on the state of health of machines. This makes it possible to anticipate necessary interventions and plan production stoppages at the most opportune moment.
This approach, known as condition-based maintenance, relies on continuous analysis of equipment to trigger maintenance operations only when they are justified by measured degradation. Unlike conventional preventive maintenance, which is based on a fixed schedule, this method limits unnecessary interventions while reducing the risk of serious breakdowns.
The benefits are manifold: reduced maintenance costs, improved machine efficiency, reduced losses due to unplanned stoppages, and optimized spare parts inventory management.
Improve safety and extend plant life
In addition to performance and reliability, vibration monitoring plays an important role in safety. A machine that is out of balance or has a mechanical fault can generate excessive vibrations that affect structural integrity, create noise nuisance or present a hazard to operators.
By continuously monitoring vibration levels, operators can identify and correct such anomalies before they endanger people or equipment. This helps to maintain a safer, more stable working environment.
In addition, by preventing progressive damage, vibration monitoring helps to extend machine life. Regular monitoring makes it possible to detect deviations as soon as they appear, and to implement targeted corrective actions, thus prolonging the profitability of industrial investments.
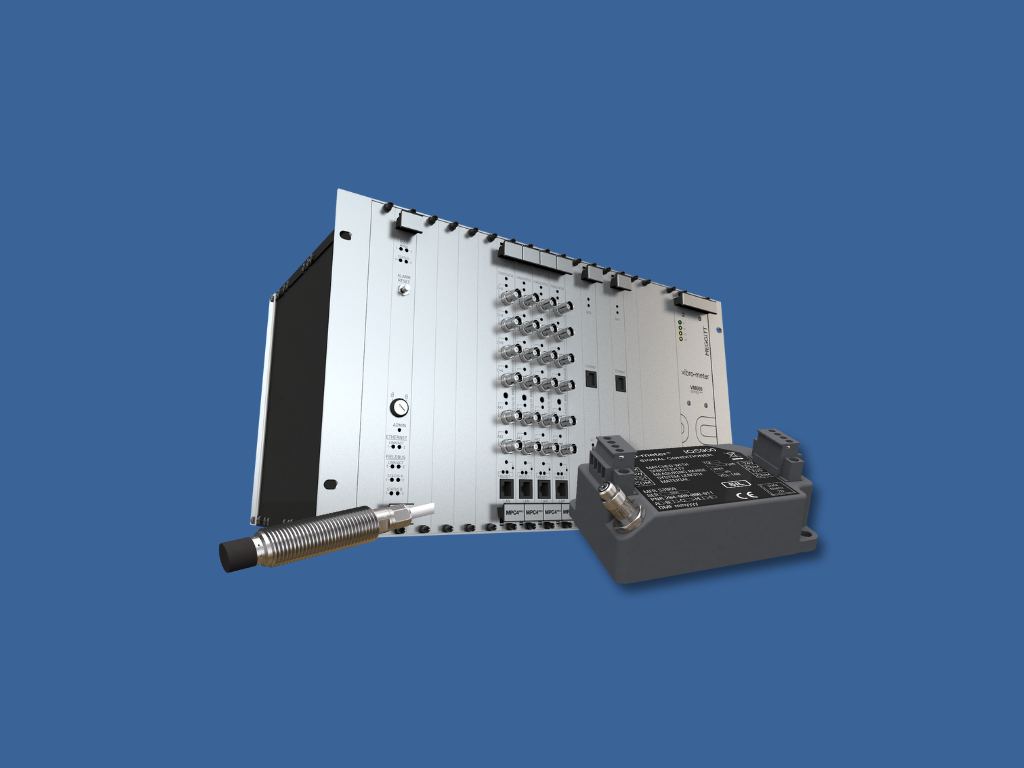
Integrate reliable tools adapted to each environment
Vibration monitoring technologies have come a long way in recent years. Specialized brands such as Parker Meggitt now offer sensors that are robust, precise and compatible with complex industrial environments (high temperature, humidity, parasitic vibrations, etc.).
This equipment can be integrated into PLCs, SCADA systems or computer-aided maintenance management (CMMS) software. They enable instantaneous visualization of data, historical recording of vibration levels, and predictive analysis based on thresholds or trends.
Choosing the right monitoring system also means ensuring compatibility with the requirements of your industry: power generation, hydraulics, petrochemicals, paper mills, or even food processing. Normandy Control Group offers tailor-made solutions, including sensor selection, installation, configuration and team training.
Why do call onNormandy Control Group/NCG ?
When you choose Normandy Control Group, you choose a partner you can trust for the maintenance and repair of your industrial equipment. As an official Woodward and Parker Meggitt (vibro-meter) distributor in France and French-speaking Africa, including Algeria, Tunisia and Morocco, we offer recognized expertise in the field. We also have two workshops in France, in Le Havre and Marseille, as well as workshops in Côte d’Ivoire and Senegal.