What’s the difference between an actuator and a controller? In complex industrial environments, where precision and reliability are paramount, it’s essential to understand the role of the various components that ensure the smooth operation of motors, turbines or generators. Two essential elements stand out in speed or position control systems: the actuator and the controller.
Although often associated in the same control chain, these two devices perform fundamentally different but complementary functions. This article will help you better understand their respective roles, interactions and importance in modern industrial applications.
The controller: the system's command center
The controller can be considered the brain of the control system. It receives information from sensors installed on the machine, analyzes it, and makes decisions in real time to adjust the equipment’s operation. Its mission is to compare a setpoint – in other words, a predefined target value – with a value measured at a given moment, in order to determine whether there is a deviation to be corrected.
Let’s take the example of an industrial combustion engine. If the engine speed exceeds or falls below the target value, the controller detects this deviation and decides to modify the fuel flow rate injected. But it doesn’t do this directly: it sends an instruction to another component, the actuator, which is responsible for carrying out the physical action.
Controllers come in a variety of forms: some are purely mechanical, as in older systems. Others are electronic, or even digital, and can incorporate advanced functions. Woodward brand controllers, widely used in industrial sectors, are a typical example of these advanced control solutions, capable of handling complex situations with great precision.
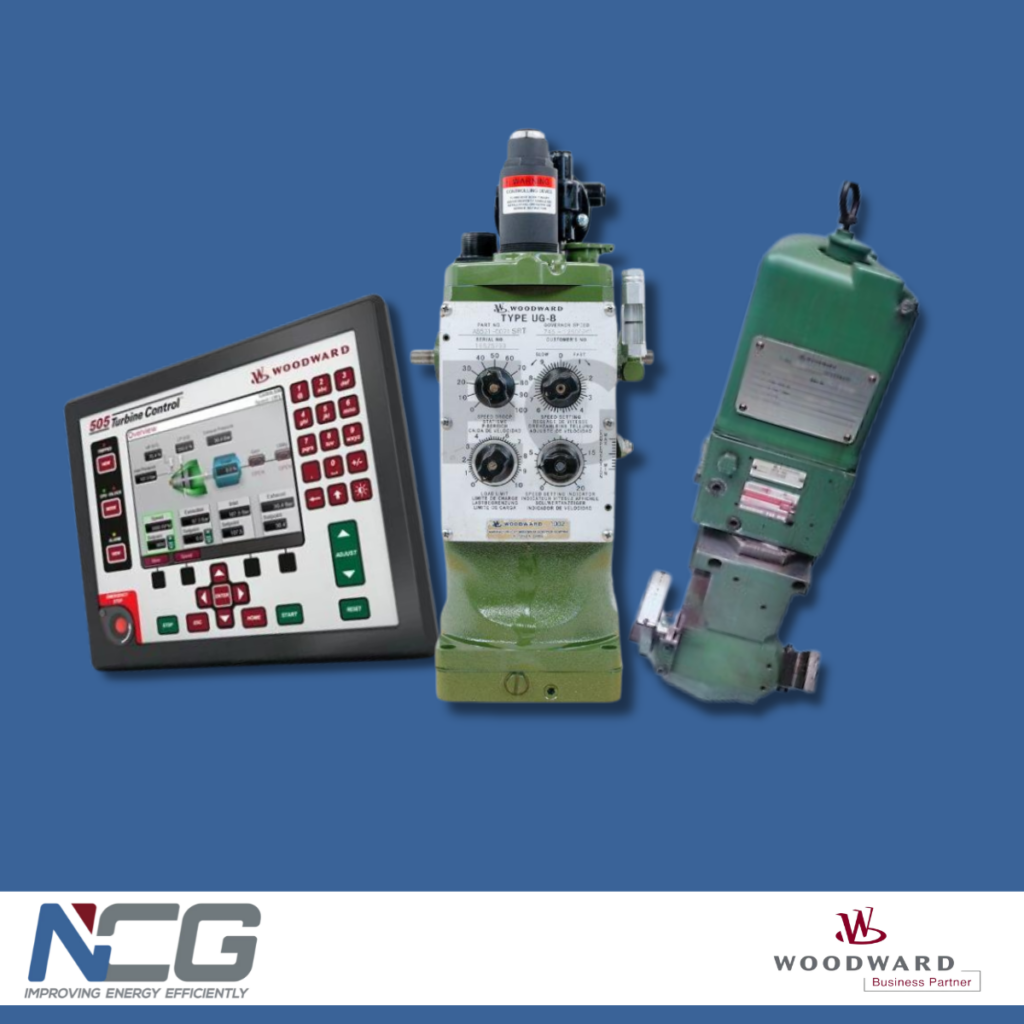
The actuator: the physical element that performs
The actuator, on the other hand, plays a very different role. It doesn’t make any decisions: it obeys. It receives a command signal, usually from the controller, and translates it into a mechanical or hydraulic movement. It is therefore the actuator that carries out the physical change required to influence the system’s behavior. This may involve opening a valve, rotating a shaft, moving a hydraulic spool, or changing the position of a fuel injector.
The technologies used in actuators are varied. There are electric actuators, which operate via motors or electromagnets; hydraulic actuators, particularly suited to applications requiring high power or extreme precision; and pneumatic actuators, which are lighter and often used in simple or mobile systems.
One of the major advantages of a good actuator is its ability to respond quickly and precisely to the commands it receives. An actuator that is too slow, unreliable or inaccurate can negate all the benefits of a high-performance controller. Conversely, even a very powerful actuator is useless if not properly controlled.
Essential collaboration between controller and actuator
The richness and complexity of a control system lies precisely in the interaction between these two components. The controller establishes a control strategy, makes decisions based on collected data and transmits them in the form of precise signals. The actuator executes them, without interpretation, by physically intervening on the machine. Together, they form a closed-loop system, in which every action is controlled, measured and adjusted in real time.
To illustrate this relationship, let’s take the example of a generator. The controller measures the frequency of the current produced, which depends directly on the motor’s rotation speed. If the frequency drops, the motor is running too slowly. The regulator then sends a command to the actuator to inject more fuel, enabling the motor to regain the right speed, and therefore a stable frequency. Once the correction has been made, the controller continues to monitor the loop, adjusting again if necessary. This process takes place continuously, sometimes hundreds of times per second.
Why is this distinction so important?
Understanding the difference between an actuator and a controller is not just of technical interest. This distinction can significantly improve plant design, fault diagnosis and preventive maintenance. A drop in performance may be due to a poorly configured controller, a damaged actuator, or a poor dialogue between the two. Identifying the source of the problem early on can prevent costly downtime or even serious failure.
Conclusion
Ultimately, in any modern control system, the controller represents intelligence, strategy and decision-making, while the actuator embodies execution, reaction and motive power. The two are inseparable, and their complementarity is essential to ensure the smooth operation of industrial machinery, whether it’s a generator, a turbine, a marine engine or production equipment.
At Normandy Control Group, we’ve made this expertise our daily business. Whether diagnosing, repairing or modernizing your control systems, we provide tailor-made solutions, adapted to the realities of the field and to the most demanding technical requirements.
Why do call on Normandy Control Group/NCG ?
When you choose Normandy Control Group, you choose a partner you can trust for the maintenance and repair of your industrial equipment. As an official Woodward and Parker Meggitt (vibro-meter) distributor in France and French-speaking Africa, including Algeria, Tunisia and Morocco, we offer recognized expertise in the field. We also have two workshops in France, in Le Havre and Marseille, as well as workshops in Côte d’Ivoire and Senegal.