In industrial sectors where turbines play a strategic role, such as power generation, petrochemicals or hydroelectric dams, monitoring their mechanical condition is crucial.
Find out what a vibration monitoring system is used for on a turbine, and why it’s essential today to guarantee the reliability, safety and profitability of installations.
A vibration monitoring system enables early identification of any sign of mechanical malfunction. By continuously measuring the vibrations generated by the turbine during operation, it detects anomalies invisible to the naked eye. This conditional approach is based on the idea that a healthy machine vibrates according to a precise pattern. Any abnormal variation in these vibrations may indicate imbalance, bearing wear, misalignment or the onset of cracking.
Understanding the usefulness of vibration monitoring on a turbine not only helps prevent major failures, but also optimizes operational performance.
Why monitor turbine vibrations?
A turbine is a complex mechanical system made up of multiple high-speed rotating parts. When an internal component begins to deteriorate, it generates vibrations different from those produced under normal conditions.
Without an appropriate monitoring system, these early signals go unnoticed. The machine continues to run until the failure becomes critical, leading to a sudden shutdown and often costly repairs.
Vibration monitoring on a turbine therefore makes it possible:
- to detect any anomalies early on
- to plan maintenance interventions before a breakdown occurs,
- to extend equipment life by avoiding premature wear,
- and to maintain productivity without unplanned interruptions.
How does a turbine vibration monitoring system work?
The principle is based on the installation of vibration sensors such as Parker Meggitt sensors at strategic points on the turbine: bearings, casings or rotation axes.
These sensors continuously record vibration levels, measuring amplitude, frequency and direction of movement.
The data is then transmitted to a centralized analysis system, capable of:
- comparing current vibrations with reference thresholds,
- establishing trends over time,
- and generating alerts if predefined limits are exceeded.
Thanks to this technology, operators can detect mechanical faults even before they are audible or visible. The usefulness of turbine vibration monitoring becomes obvious: it transforms reactive maintenance into predictive maintenance, which is much more economical and safer.
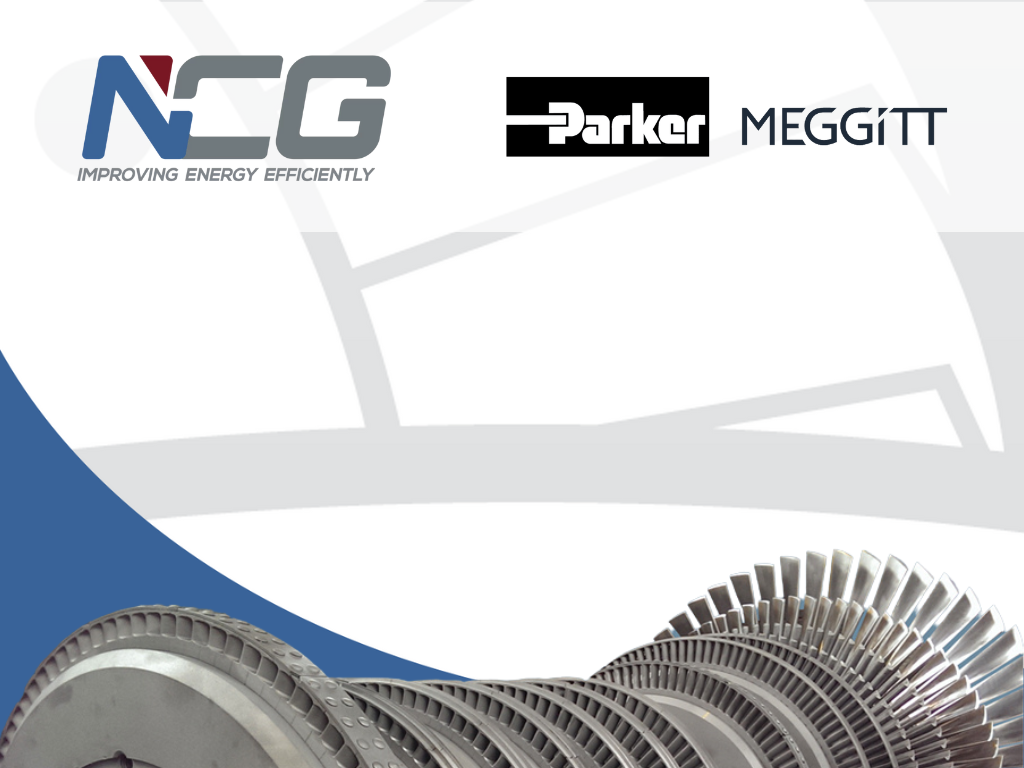
What problems can vibration monitoring detect?
Vibration monitoring systems can detect a wide range of mechanical problems on turbines, including:
- Rotor imbalances,
- Shaft misalignment,
- Excessive bearing play,
- Internal structural cracks,
- Wear or lubrication failure.
Each problem generates a specific “vibration profile”. Through detailed analysis, it is possible not only to identify that a problem exists, but also to determine its likely nature.
In this way, vibration monitoring on a turbine is more than just an anomaly detector: it’s a fast, accurate diagnostic tool.
Why do call on Normandy Control Group/NCG ?
When you choose Normandy Control Group, you choose a partner you can trust for the maintenance and repair of your industrial equipment. As an official Woodward and Parker Meggitt (vibro-meter) distributor in France and French-speaking Africa, including Algeria, Tunisia and Morocco, we offer recognized expertise in the field. We also have two workshops in France, in Le Havre and Marseille, as well as workshops in Côte d’Ivoire and Senegal.