A technical solution to optimize turbine management
Adapting control systems is essential to guarantee the performance and safety of industrial installations. Recently, our teams were called in to modify the operation of a Woodward 505XT controller, switching from power regulation mode to power limitation. This technical transformation enables us to optimize turbine management in line with new operating constraints.
Understanding the difference between regulation and power limitation
A power controller like the Woodward 505XT is designed to adjust the level of power supplied by a turbine according to the needs of an industrial system. It operates in a closed loop, continuously adapting power production to demand.
However, in certain configurations, it becomes necessary to modify this operating mode to introduce a power limitation. This approach imposes a maximum power threshold that the turbine cannot exceed, regardless of load variations. The main aim is to prevent overloads, reduce equipment wear and tear, and improve long-term plant reliability.
Why this change?
There are several reasons for optimizing control systems:
- Compliance with new operational constraints: some installations have to comply with strict energy limitation rules in order to preserve infrastructure or meet environmental standards.
- Improved safety: power limiting prevents the risk of overload and protects the whole system from extreme fluctuations.
- Optimized performance: power limiting ensures greater energy efficiency and lower maintenance costs.
- Longer equipment life: by avoiding overload phases and sudden variations, mechanical and electronic components wear out less quickly.
High-precision technical intervention
Reprogramming the Woodward 505XT requires advanced expertise in control systems and industrial automation. Here are the main stages of our intervention:
- Analysis of requirements and operating context: prior to any intervention, we carried out an in-depth study of the site and the turbine’s technical specifications. This phase enabled us to define the optimum parameters for the reconfiguration.
- Reconfiguration of controller parameters: power thresholds were adjusted to limit energy output while maintaining a stable response to load variations.
- Real-life tests: we carried out several tests to verify the compliance of the new parameters. These included load simulations and dynamic checks.
- Validation and commissioning: once the system’s performance and safety had been validated, the modification was deployed in production.
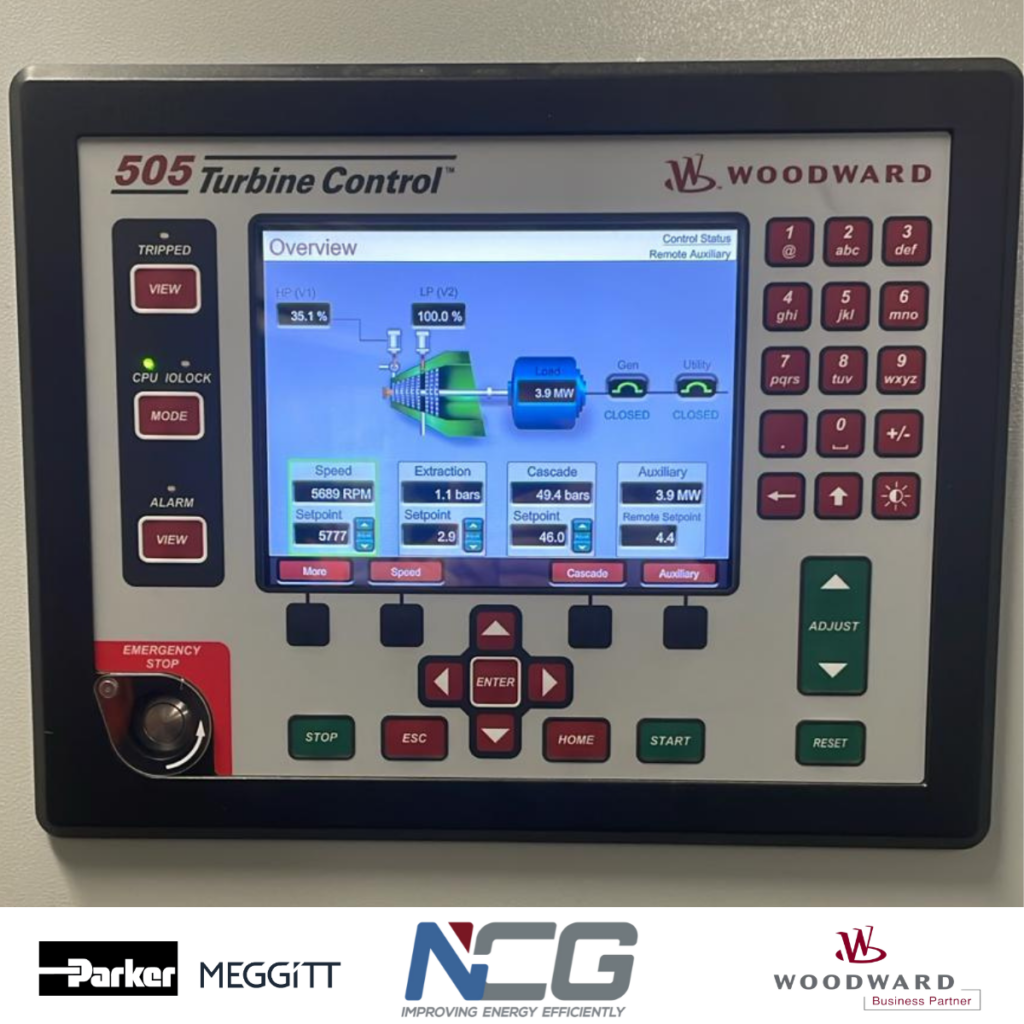
Why do call on Normandy Control Group/NCG ?
When you choose Normandy Control Group, you choose a partner you can trust for the maintenance and repair of your industrial equipment. As an official Woodward and Parker Meggitt (vibro-meter) distributor in France and French-speaking Africa, including Algeria, Tunisia and Morocco, we offer recognized expertise in the field. We also have two workshops in France, in Le Havre and Marseille, as well as workshops in Côte d’Ivoire and Senegal.